POLYSTYRENE
ABOUT - CLIMATE
CHANGE - CROWDFUNDING
- CONTACTS - DONATE
- FOUNDATION -
OCEAN CLEANUP
- HOME - A-Z INDEX
SINGLE
USE PLASTICS - This is
just a small sample of the plastic packaging that you will
find in retails stores all over the world. A good proportion
of this packaging - around 8 millions tons a year, will end up
in our oceans, in the gut of the fish
we eat, in the stomachs
of seabirds and in the intestines of whales and other marine
mammals. Copyright photograph © 22-7-17 Cleaner
Ocean Foundation Ltd, all rights
reserved.
Although it is a closed-cell foam, both expanded and extruded polystyrene are not entirely waterproof or vaporproof. In expanded polystyrene there are interstitial gaps between the expanded closed-cell pellets that form an open network of channels between the bonded pellets, and this network of gaps can become filled with liquid water. If the water freezes into ice, it expands and can cause polystyrene pellets to break off from the foam. Extruded polystyrene is also permeable by water molecules and can not be considered a vapor barrier.
Waterlogging commonly occurs over a long period of time in polystyrene foams that are constantly exposed to high humidity or are continuously immersed in water, such as in hot tub covers, in floating docks, as supplemental flotation under boat seats, and for below-grade exterior building insulation constantly exposed to groundwater. Typically an exterior vapor barrier such as impermeable plastic sheeting or a sprayed-on coating is necessary to prevent saturation.
Polystyrene is a synthetic aromatic hydrocarbon polymer made from the monomer styrene. Polystyrene can be solid or foamed. General-purpose polystyrene is clear, hard, and rather brittle. It is an inexpensive resin per unit weight. It is a rather poor barrier to oxygen and water vapour and has a relatively low melting point. Polystyrene is one of the most widely used plastics, the scale of its production being several million tonnes per year. Polystyrene can be naturally transparent, but can be coloured with colourants. Uses include protective packaging (such as packing peanuts and CD and DVD cases), containers (such as "clamshells"), lids, bottles, trays, tumblers, disposable cutlery and in the making of models.
As a thermoplastic polymer, polystyrene is in a solid (glassy) state at room temperature but flows if heated above about 100 °C, its glass transition temperature. It becomes rigid again when cooled. This temperature behaviour is exploited for extrusion (as in Styrofoam) and also for molding and vacuum forming, since it can be cast into molds with fine detail.
Polystyrene is slow to biodegrade and is therefore a focus of controversy among environmentalists. It is increasingly abundant as a form of litter in the outdoor environment, particularly along shores and waterways, especially in its foam form, and also in increasing quantities in the Pacific Ocean.
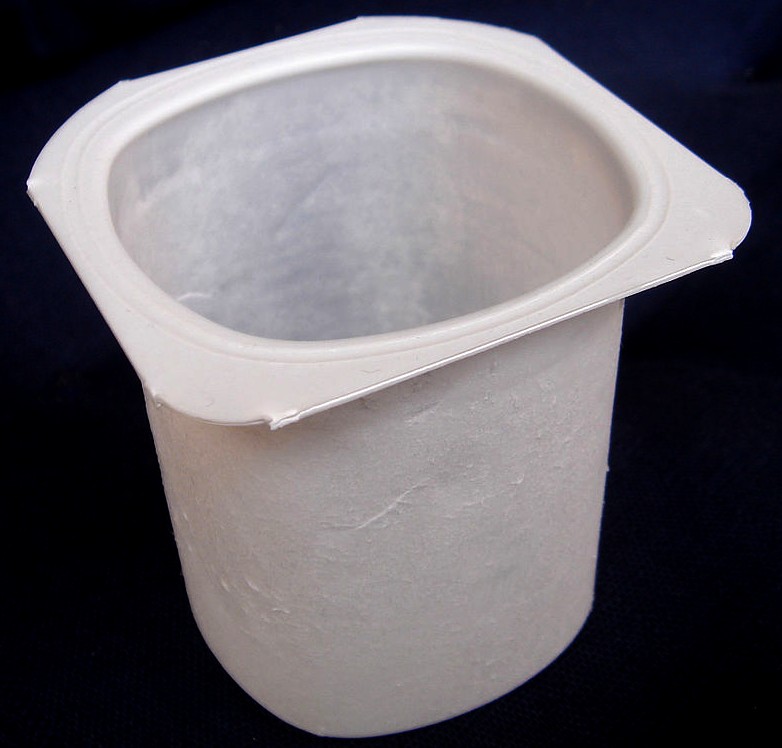
Polystyrene is chemically very inert, being resistant to acids and bases but is easily dissolved by many chlorinated solvents, and many aromatic hydrocarbon solvents. Because of its resilience and inertness, it is used for fabricating many objects of commerce. It is attacked by many organic solvents, which dissolve the polymer. Foamed polystyrene is used for packaging chemicals.
Like all organic compounds, polystyrene burns to give carbon dioxide and
water vapor. Polystyrene, being an aromatic hydrocarbon, typically combusts incompletely as indicated by the sooty flame.
Polystyrene is commonly injection molded, vacuum formed, or extruded, while expanded polystyrene is either extruded or molded in a special process. Polystyrene copolymers are also produced; these contain one or more other monomers in addition to styrene. In recent years the expanded polystyrene composites with cellulose and starch have also been produced. Polystyrene is used in some polymer-bonded explosives (PBX).
EXPANDED
POLYSTYRENE
.Expanded polystyrene (EPS) is a rigid and tough, closed-cell foam with a normal density range of 11 to 32 kg/m3. It is usually white and made of pre-expanded polystyrene beads. EPS is used for many applications e.g. trays, plates, bowls and fish boxes. Other uses include molded sheets for building insulation and packing material ("peanuts") for cushioning fragile items inside boxes. Sheets are commonly packaged as rigid panels (size 4 by 8 or 2 by 8 feet in the United States).
Due to its technical properties such as low weight, rigidity, and formability, EPS can be used in a wide range of applications. Sales are likely to rise to more than US$15 billion by 2020.
Thermal conductivity is measured according to EN 12667. Typical values range from 0.032 to 0.038 W/(m·K) depending on the density of the EPS board. The value of 0.038 W/(m·K) was obtained at 15 kg/m3 while the value of 0.032 W/(m·K) was obtained at 40 kg/m3 according to the data sheet of K-710 from StyroChem Finland. Adding fillers (graphites,
aluminium, or carbons) has recently allowed the thermal conductivity of EPS to reach around 0.030–0.034 (as low as 0.029) and as such has a grey/black colour which distinguishes it from standard EPS. Several EPS producers have produced a variety of these increased thermal resistance EPS usage for this product in the
UK &
EU.
Water vapor diffusion resistance (μ) of EPS is around 30–70.
ICC-ES (International Code Council Evaluation Service) requires EPS boards used in building construction meet ASTM C578 requirements. One of these requirements is that the oxygen index of EPS as measured by ASTM D2863 be greater than 24 volume %. Typical EPS has an
oxygen index of around 18 volume %; thus, a flame retardant is added to styrene or polystyrene during the formation of EPS.
The boards containing a flame retardant when tested in a tunnel using test method UL 723 or ASTM E84 will have a flame spread index of less than 25 and a smoke-developed index of less than 450. ICC-ES requires the use of a 15-minute thermal barrier when EPS boards are used inside of a building.
According to EPS-IA ICF organization, the typical density of EPS used for insulated concrete forms is 1.35 to 1.80 pcf. This is either Type II or Type IX EPS according to ASTM C578. EPS blocks or boards used in building construction are commonly cut using hot wires.
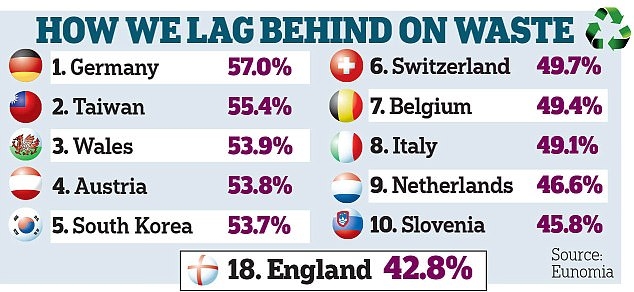
HISTORY
Polystyrene was discovered in 1839 by Eduard Simon, an apothecary from Berlin. From storax, the resin of the American sweetgum tree Liquidambar styraciflua, he distilled an oily substance, a monomer that he named styrol. Several days later, Simon found that the styrol had thickened into a jelly he dubbed styrol oxide ("Styroloxyd") because he presumed an oxidation. By 1845 Jamaican-born chemist John Buddle Blyth and German chemist August Wilhelm von Hofmann showed that the same transformation of styrol took place in the absence of oxygen. They called the product "metastyrol"; analysis showed that it was chemically identical to Simon's
Styroloxyd. In 1866 Marcelin Berthelot correctly identified the formation of metastyrol/Styroloxyd from styrol as a polymerisation process. About 80 years later it was realized that heating of styrol starts a chain reaction that produces macromolecules, following the thesis of German organic chemist Hermann Staudinger (1881–1965). This eventually led to the substance receiving its present name, polystyrene.
The company I. G. Farben began manufacturing polystyrene in Ludwigshafen, about 1931, hoping it would be a suitable replacement for die-cast zinc in many applications. Success was achieved when they developed a reactor vessel that extruded polystyrene through a heated tube and cutter, producing polystyrene in pellet form.
In 1941, Dow Chemical invented a Styrofoam process.
Before 1949, chemical engineer Fritz Stastny (1908–1985) developed pre-expanded PS beads by incorporating aliphatic hydrocarbons, such as pentane. These beads are the raw material for moulding parts or extruding sheets. BASF and Stastny applied for a patent that was issued in 1949. The moulding process was demonstrated at the Kunststoff Messe 1952 in Düsseldorf. Products were named Styropor.
The crystal structure of isotactic polystyrene was reported by Giulio Natta.
In 1954, the Koppers Company in Pittsburgh, Pennsylvania, developed expanded polystyrene (EPS) foam under the trade name Dylite. In 1960, Dart Container, the largest manufacturer of foam cups, shipped their first order.
LINKS
& REFERENCE
https://
FOAM
& BOTTLES - Expanded polystyrene is
used to package household electrical goods, while soft drinks and water is
sold in PET plastic bottles by the billions every year. The numbers are
staggering. It's no wonder then that some of this plastic will end up on our
plate in one form or another, potentially as a toxin carrier. Copyright
photograph © 22-7-17 Cleaner Ocean Foundation Ltd, all rights reserved. Animals do not recognize polystyrene foam as an artificial material and may even mistake it for food. Polystyrene foam blows in the wind and floats on water, due to its low specific gravity. It can have serious effects on the health of birds or marine animals that swallow significant quantities.
ABS
- BIOMAGNIFICATION
- BP DEEPWATER - CANCER
- CARRIER BAGS
- CLOTHING - COTTON BUDS - DDT - FISHING
NETS
FUKUSHIMA - HEAVY
METALS - MARINE LITTER
- MICROBEADS
- MICRO
PLASTICS - NYLON - OCEAN GYRES
- OCEAN WASTE
PACKAGING - PCBS
-
PET - PETROLEUM
- PLASTIC
- PLASTICS
- POLYCARBONATE
- POLYOLEFINS - POLYSTYRENE
- POLYPROPYLENE - POLYTHENE - POPS
-
PVC - SHOES
- SINGLE USE
- SOUP - STRAWS - WATER
This
website is provided on a free basis as a public information
service. copyright © Cleaner
Oceans Foundation Ltd (COFL) (Company No: 4674774)
2018. Solar
Studios, BN271RF, United Kingdom.
COFL
is a charity without share capital.
|